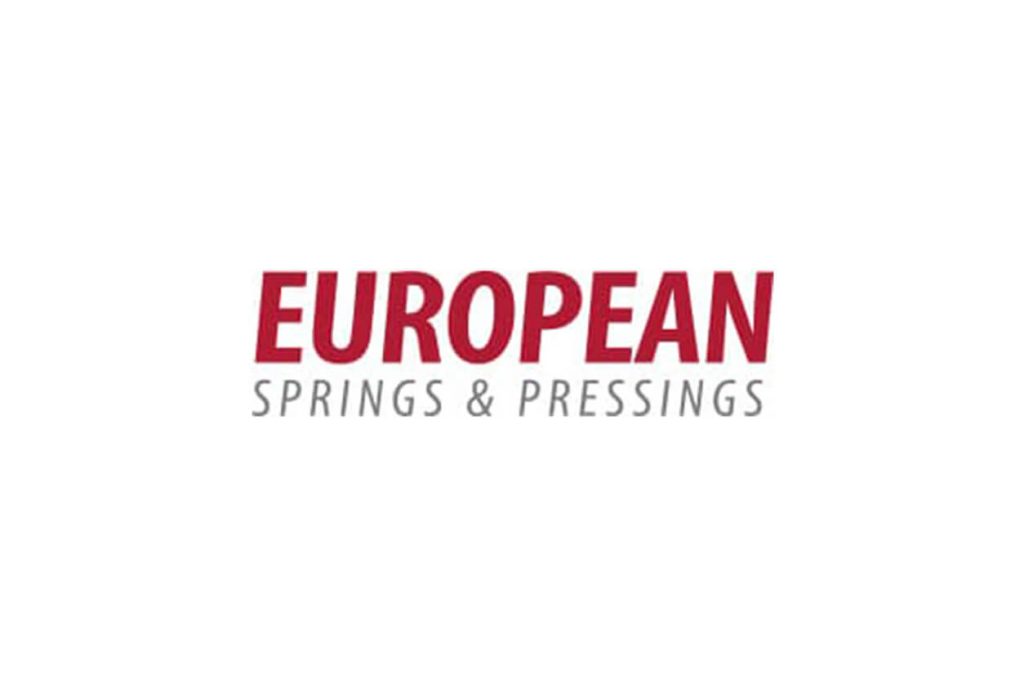
The UK Encourages More Young People to be Engineers than Bankers
Here at European Springs Ireland, we love hearing about young people getting into engineering. After all, we do need the
Home › Engineering › Page 13
Here at European Springs Ireland, we love hearing about young people getting into engineering. After all, we do need the
When it comes to our love of engineering at European Springs IE, we aren’t just about die springs and pressings…
To say that we are easily excited when we hear about any new engineering feat is an understatement, and one
Technology is advancing at an alarming rate and with more people requiring prosthetic limbs to be able to get on
Scientists have been looking to nature to help solve engineering problems for years – and now they’ve turned their attention
Engineering UK have recently hired two video bloggers ‘vloggers’ to help inspire the new generation of engineers. After a huge
No, we aren’t predicting the next Terminator film, we’re commenting on the news that has been driving scientific media wild
These days, most of us don’t think twice about the towering buildings that fill our cities’ skylines; most skyscrapers barely
At European Springs Ireland, we aren’t your average spring manufacturer and we love seeing how engineering benefits other industries, and how
And even if we don’t have exactly the tool we need, European Springs’ in house technology enables us rapidly to design and make complex tools, allowing us to offer more competitive prices.
© Copyright 2025 | European Springs
Designed, Promoted and Powered by SQ Digital